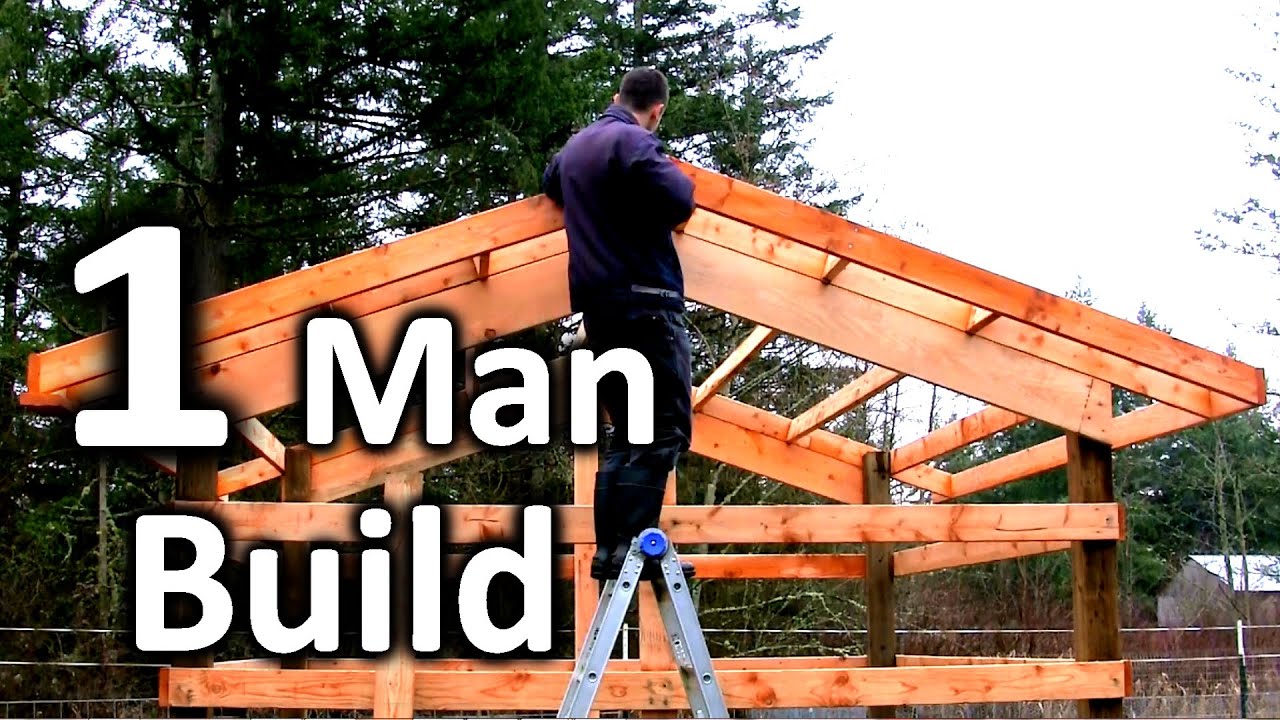
A pole barn, also known as a post-frame building, offers a versatile and cost-effective construction solution for a variety of uses, from agricultural storage to workshops and even residential homes. This guide provides a detailed, step-by-step approach to constructing a pole barn featuring durable and low-maintenance steel siding.
I. Planning and Preparation:
A. Design and Drawings:
1. Define the Purpose: Determine the primary use of your pole barn. This will dictate the size, layout, and structural requirements.
2. Assess the Site: Consider the terrain, drainage, and access points. Ensure the chosen location meets local zoning regulations and building codes.
3. Develop a Plan: Create detailed drawings, including the floor plan, elevations, and roof design. Include dimensions, door and window placements, and any desired interior features.
4. Consult Professionals: Seek advice from engineers and architects to ensure your design is structurally sound and compliant with local codes.
B. Material Selection:
1. Posts: Select pressure-treated wood poles or steel posts for durability and resistance to rot and insect damage. The size and spacing of the posts will depend on the building's size, snow load, and wind conditions.
2. Framing: Use dimensional lumber or engineered wood products for the rafters, trusses, and wall framing. Consider factors like span, snow load, and desired insulation.
3. Siding: Steel siding offers excellent durability, fire resistance, and low maintenance. Choose from various styles and finishes, including corrugated, ribbed, or painted options.
4. Roofing: Select a metal roof for its durability, longevity, and low maintenance. Options include standing seam, corrugated, or metal shingles.
5. Windows and Doors: Choose energy-efficient windows and doors, considering the size and placement based on the intended use and climate.
C. Permits and Inspections:
1. Obtain Permits: Check local building codes and apply for necessary permits for construction.
2. Schedule Inspections: Arrange for inspections at various stages of construction, such as foundation and framing inspections.
II. Foundation Construction:
A. Site Preparation:
1. Clear the Area: Remove any vegetation, debris, and existing structures.
2. Level the Ground: Use a laser level or surveyor's transit to achieve a level and compacted surface.
3. Install a Gravel Base: Lay a layer of gravel, typically 4-6 inches deep, to provide drainage and support for the concrete piers.
B. Concrete Pier Construction:
1. Excavate Pier Holes: Dig holes for the concrete piers based on the dimensions and spacing specified in the design plans.
2. Install Forms: Create forms using plywood or steel to define the shape and size of the piers.
3. Pour Concrete: Mix and pour concrete into the forms, ensuring proper compaction and leveling.
4. Curing: Allow the concrete to cure properly before removing the forms, following the manufacturer's recommendations.
III. Pole Installation and Framing:
A. Pole Installation:
1. Set the Poles: Carefully position the posts in the pre-drilled concrete pier holes, ensuring they are plumb and level.
2. Secure the Poles: Use concrete anchors, bolts, or steel plates to secure the poles to the concrete piers.
3. Adjust and Level: Double-check the posts for plumb and level, making any necessary adjustments before securing them permanently.
B. Framing Construction:
1. Attach Bottom Plates: Secure bottom plates to the posts using structural screws or nails, creating the foundation for the wall framing.
2. Erect Wall Framing: Install the wall framing members, ensuring they are properly spaced and fastened to the bottom plates and top plates.
3. Install Rafters or Trusses: Construct the roof framing using prefabricated trusses or by framing individual rafters according to the design plans.
4. Sheathing: Install sheathing boards over the framing, providing a structural base for the siding and roofing.
IV. Siding Installation:
A. Underlayment:
1. Install Housewrap: Apply a water-resistant housewrap over the sheathing to create a moisture barrier and enhance insulation.
2. Attach Furring Strips: Install furring strips over the housewrap, creating a ventilated air space between the siding and sheathing.
B. Siding Application:
1. Start at the Bottom: Begin installing the steel siding from the bottom row, working upwards.
2. Secure Panels: Use self-drilling screws or rivets to attach the steel siding panels to the furring strips.
3. Overlap Panels: Ensure panels overlap according to the manufacturer's instructions, providing a weather-tight seal.
4. Install Trim: Install trim pieces around windows, doors, and corners, creating a finished appearance.
V. Roof Installation:
A. Roof Underlayment:
1. Install Roofing Felt: Place a layer of roofing felt over the sheathing, creating a waterproof barrier.
2. Install Ice and Water Shield: Install ice and water shield along the eaves and roof edges to prevent water damage from ice dams.
B. Metal Roofing Installation:
1. Install Metal Panels: Start at the bottom of the roof and work upwards, securing the metal panels to the rafters or trusses.
2. Overlap Panels: Ensure panels overlap properly, following the manufacturer's instructions.
3. Install Flashing: Install flashing around chimneys, vents, and other roof penetrations to prevent water leakage.
4. Install Ridge Cap: Complete the roof installation by attaching a ridge cap along the peak of the roof.
VI. Finishing Touches:
A. Interior Finishes:
1. Install Insulation: Insulate the walls and ceiling to improve energy efficiency.
2. Install Drywall or Paneling: Finish the interior walls and ceiling with drywall, plywood paneling, or other desired materials.
3. Install Flooring: Choose flooring suitable for the intended use, such as concrete, wood, or epoxy.
B. Exterior Finishes:
1. Install Gutters and Downspouts: Install gutters and downspouts to direct water away from the building.
2. Paint or Stain: Paint or stain the trim and doors according to your aesthetic preferences.
3. Install Landscaping: Enhance the exterior with landscaping features, including trees, shrubs, and walkways.
VII. Maintenance and Care:
A. Regular Inspections: Inspect the pole barn periodically for signs of damage or deterioration, such as leaks, loose fasteners, or rust.
B. Cleaning and Maintenance: Clean the exterior regularly to remove dirt and debris.
C. Roof Maintenance: Inspect the roof for any missing or damaged shingles, and repair as needed.
Conclusion:
Building a pole barn with steel siding offers a durable, cost-effective, and low-maintenance construction solution. By carefully following these steps, you can create a versatile structure tailored to your specific needs. Remember to always prioritize safety, obtain necessary permits, and consult with professionals when needed. With proper planning and execution, your pole barn will serve you well for many years to come.
No comments:
Post a Comment
Note: Only a member of this blog may post a comment.